GOLDEN TUSSAR SILK - HAND SPUN & HANDWOVEN FROM ODISHA , INDIA.
About the Tussar (or Tussah) silk & the process:
Cocoons are collected from the wild then hung on Arjuna trees, where they hatch naturally until the tree has been stripped of the foliage (they move them to another tree if that's the case). During the larval stage (up to 7 weeks) guard is kept against the insects and natural enemies such as bats, birds and beetles. The caterpillars eat constantly, growing to over 12 times their original size in as little as 30 days. When they are ready, the caterpillars begin making their cocoons. The cocoons are made from single, continuous filaments of silk produced by the salivary glands.
On completion the cocoons are harvested like fruit. The cocoons aren't like other silk moths, they're almost like hard eggshells with a very distinct stem where the cocoon is attached to the branch. Each slightly is a different colour depending on what the insect ate. Some are light green, yellow, some grey and others are almost white. Dyers will appreciate that the shades of the cocoon (the silk) is the result of tannins in the leaves ingested by larvae.
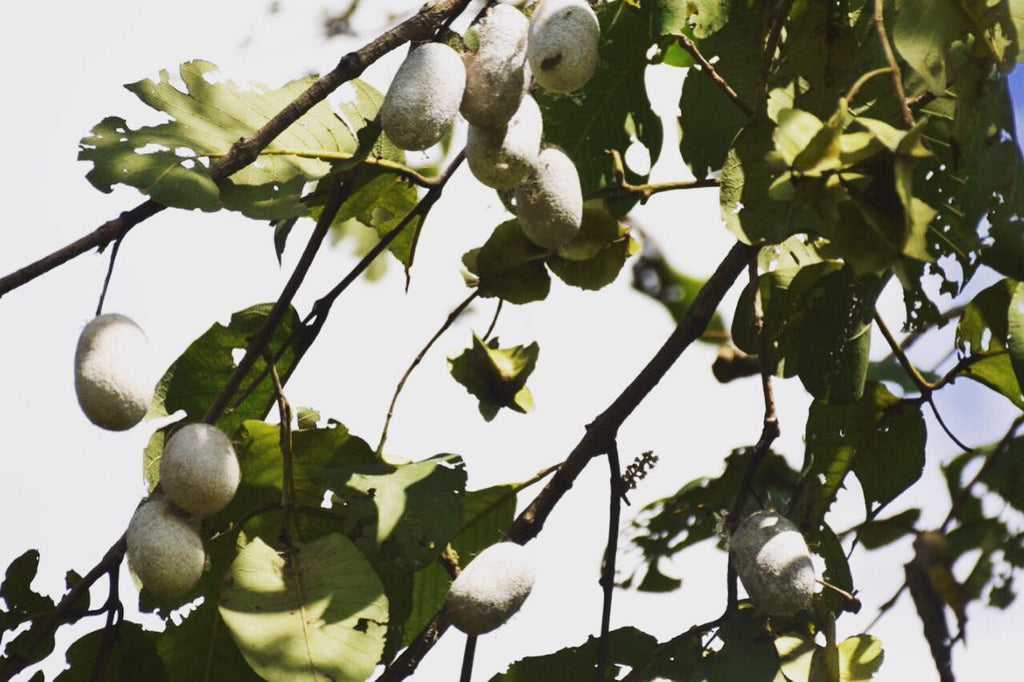
When the adult moth emerges from the cocoon it needs to make a hole to get out. The cocoon from which adults emerge is known as 'pierced' because of this hole. The hole cuts many of the fibres so that the silk from pierced cocoons can't be reeled. The silk is still used but it is spun like cotton or wools and forms a lower grade of silk. In the village I stayed they use a lot of the pierced silk, this is spun and used for the ghicha yarn and woven into ghicha fabric. This is also known as 'peace' silk as the moth hasn't be harmed.
The cocoons are placed in warm water to loosen the gum (Sericin) that holds it together. The heating is an important part in the manufacturing of silk as it softens the cocoon and makes the extraction of silk easier. One strand of silk is incredibility thin and would be too weak for most textiles so serveral cocoons are hand rolled together or reeled together to bind them together to make one thread.
Over 4,000 cocoons are needed for every 450grams of reeled silk.
Tussar moths have the ability to fly, unlike domesticated moths which can't fly, and they have a wingspans of 15cm.

The fibres are naturally a browny gold colour that sets it apart from most other silks, hence the name 'golden silk'. The colour is tantalisingly close to metallic, especially when the warps are on the loom. Amazing the silk doesn't lose its luster in the dying process. The yarn is coarse, strong and durable with a natural, dull golden colour and rich texture. It is suitable for weaving, knitting, crocheting and plying with another fibre. Prices varies depending on weight and grade.
In Odisha and many parts of India fabrics are woven by hand with large beaters. This gives the fabric more of a sheen and natural organic feeling. Cotton silk and paper silk are made on a power loom because the yarns are too fine.
Coloured thread in weave is a mark of joinery of the weft yarn. The weaves do this when weft yarn falls short and another weft yarn is joined. In order to maintain the quality, the coloured thread can be removed with a sharp needle or left depending on the buyer.
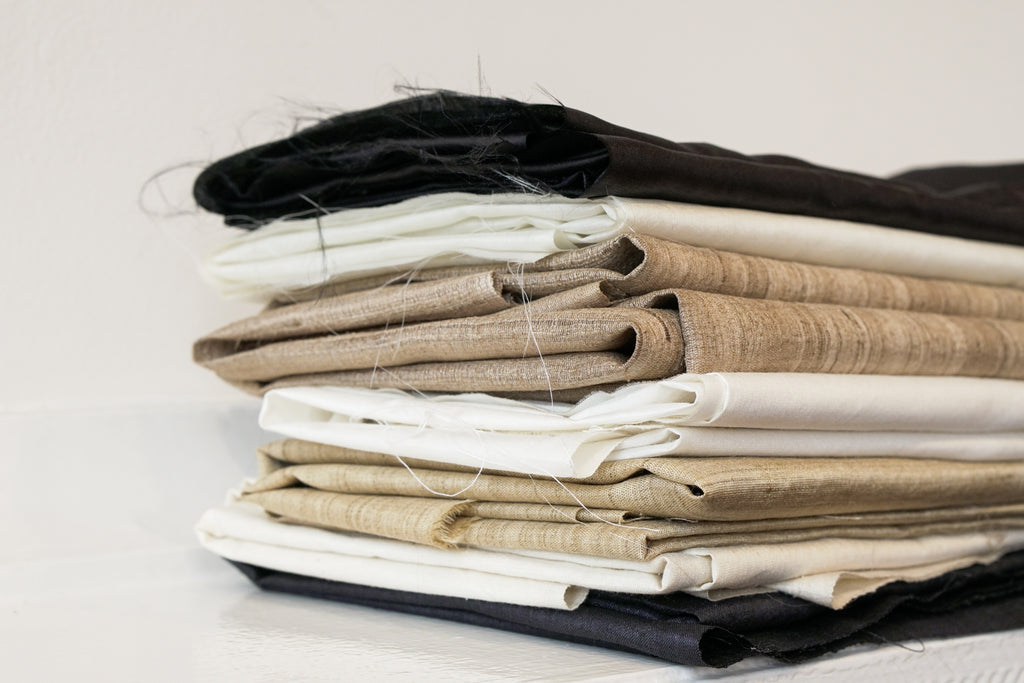
About my experience:
I undertook a three month art residency 'D.I.S.C: The Art Textile Program Link, The Never Ending Thread" in 2017 in Odisha, India. During the residency I lived in a small rural village called Fakirpur which is on the outskirts of Bhubaneswar.
It was an invaluable experience for me. It lead to me learning new techniques and my passion for textiles was rejuvenated. This was my first trip to India and won't be the last.
Before the trip I had never heard of Wild Tussar Silk or knew much about hand spinning or hand weaving. It was a new world for me but I fell IN LOVE with the Tussar silk and the village. This has now resulted in me selling the material and yarn in Australia and I'm experimenting with new projects at the moment which I'm very excited about.
The people of Fakirpur welcomed me their beautiful village and homes, sharing their knowledge of Tussar silk and how the cloth is made, something I didn't learn during my time at fashion school and its a link I think is very important and missing in the fashion industry. I was shown stages of the Tussar silk process from the early stages of farming the silk in the nearby forests, sharing the Tussar between the village, spinning, dying and to the end result of woven, finished material /cloth.
This rich experience has driven me to learn more about Tussar silk, to help the village, sustain, grow and employ others to continue to make Tussar products. Rural farmers require, our investment . It provides income and employment to the rural village who are quite poor and unemployment when there's is no farming in rice fields . Tussar faces the same issues as other weavers. The younger generations do not want to invest so much time and effort and the charm of beautiful silk is slowly losing out.
Shelly Tindale
Owner / Artist / Designer at Tindale Designs.
Owner / Artist / Designer at Tindale Designs.